to Metals
to Coating technologies
Electrochemical machining is a process of a selective dissolution of the anodically connected work piece material submerged in an electrolyte together with an anodically connected tool.
Principally electrochemical machining is similar to Electropolishing where the work piece surface roughness decreases due to the conversion of the atoms into ions and their removal from the surface as a result of a passage of an electric current.
Electrochemical machining is generally opposite to electroplating where the metallic ions traveling through the electrolyte solution deposit on the surface of the cathodically connected work piece.
The electrochemical reactions occurring in the electrochemical machining process are as follows:
At the anode the iron atoms covert into the iron ions (cations):
Fe = Fe2+ + 2e-
The electrons lost by the iron atoms travel to the cathode through the DC power supply.
At the cathode the electrons react with water molecules forming gaseous Hydrogen and hydroxyl ions (anions) according to the reaction:
H2O + 2e- = H2 + 2OH-
The cations and the anions react in the aqueous solution and create insoluble ferrous hydroxide:
Fe2+ + 2OH- = Fe(OH)2
The insoluble hydroxide is taken away by the flowing electrolyte and then it precipitates at the tank bottom forming the sludge.
The principle scheme of electrochemical process is presented in the figure below.
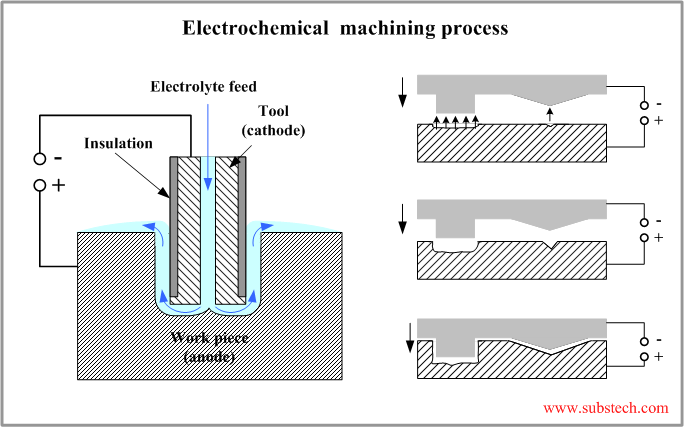
The work piece is mounted in a fixture electrically isolated from the tank and other machine parts. The work piece is connected to the positive terminal (anode) of the Power Supply. The tool is connected to the negative terminal (cathode).
The electrolyte is continuously flowing through a hole in the tool to the gap between the work piece and the tool surfaces.
The tool is moving towards the work piece at a constant speed of about 0.05”/min (1.25 mm/min). The gap between the tool and the work piece is kept constant. Stable behavior of the process is a result of a control of the power supply voltage.
The final shape of the work piece formed as a result of the electrochemical machining process conforms the shape of the tool.
Electrolytes used in electrochemical machining:
Sodium chloride (
NaCl) at the concentration of 20% - for ferrous alloys(e.g.
Steels and cast irons and cobalt alloys.
Sodium nitrate (NaNO3) - for ferrous alloys.
-
A mixture of sodium chloride (NaCl) and sulfuric acid (H2SO4) - for nickel alloys.
A mixture of 10% hydrofluoric acid (
HF), 10% hydrochloric acid (
HCl), 10% nitric acid (
HNO3) - for
Titanium alloys.
Sodium hydroxide (NaOH) - for tungsten carbide (WC).
to top
An industrial electrochemical machining unit consists of the following systems:
DC Power supply. The machining rate in electrochemical machining is proportional to the electric current density. In order to achieve high values of the machining rate electrochemical machining is commonly performed at a high direct current exceeding 1000 A. The voltage of the process is 5-25 V.
Electrolyte circulation system. The products of the electrochemical reaction should be removed from the gap between the work piece and the tool. Accumulation of the reaction products causes decrease of the process efficiency and reduction of the rate of machining. Therefore the electrolyte flow speed should be high. Commonly it is in the range 1,000-10,000 ft/min ( 300-3,000 m/min). The electrolyte is continuously filtered in order to trap the precipitated reaction products (sludge).
Mechanical system. One of the most important parameters of electrochemical machining is maintaining a constant voltage level. This is achieved by the control system providing a movement of the tool at a constant speed equal to the linear rate of machining. The process in a steady state is performed at a constant (typically gap 0.004-0.016”/0.1-0.4 mm). A firm fixation of the work piece provided by the fixture, the table and the frame is also important for stable operation of the system at a constant gap. Conventional machining equipment including CNC machines may be modified for electrochemical machining process.
Control system. Electrical parameters of the process, , tool feed speed and parameters of electrolyte circulation system are controlled by the control system, which provide stable and efficient operation of the unit.
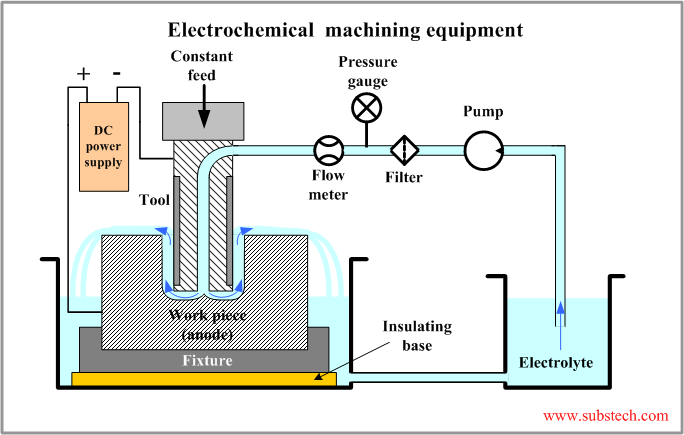
to top
Machining of hard materials. The process parameters and the tool life time do not depend on the
hardness of the work piece therefore electrochemical machining is often used for machining hard materials. Turbine blades and rifle barrels are fabricated by electrochemical machining.
Producing holes and cavities which can not be obtained by conventional machining methods.
Die sinking. Electrochemical machining is often used as an alternative to the cavity type electric discharge machining (EDM).
Fabrication of thin walled parts. Electrochemical machining does not produce surface stress in the work piece therefore even very brittle and easily deformed materials may be machined in thin walled shapes.
Grinding of a work piece by a rotating wheel, which performs grinding operation through an electrolyte. The wheel is conductive and cathodically connected. Non-conductive hard particles are set on the wheel surface. The particles provide a constant gap through which an electrolyte is continuously fed. Hard and brittle materials are ground by the method.
to top
Advantages of electrochemical machining:
The rate of machining does not depend on the
hardness of the work piece material.
The tool does not wear. Soft materials (e.g.,
copper) may be used for tool fabrication.
No stresses are produced on the work piece surface.
No burrs form in the machining operation.
High surface quality may be achieved.
High accuracy of the machining operation.
Disadvantages of electrochemical machining:
Higher cost.
Electrolyte may cause
corrosion of the equipment.
Large production floor is required.
Only electrically conductive materials may be machined.
Not environmentally friendly process.
to top